반응형
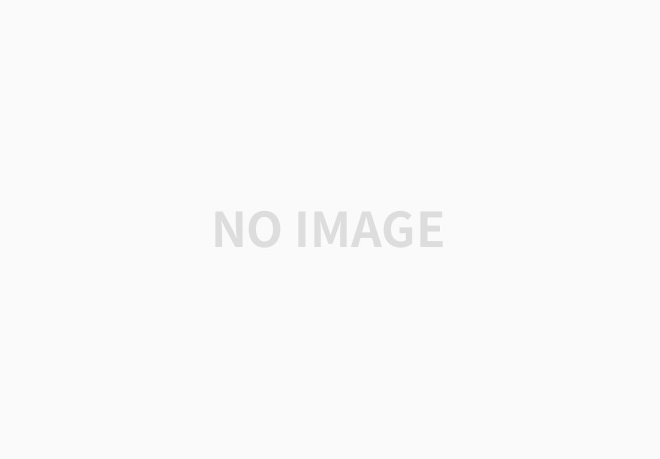
미세화 트랜드에 따라 ALD의 비중은 점점 더 중요해지고 있습니다. ALD와 관련된 예상질문들을 정리해보았습니다.
[질문 1]. 가볍게 'ALD'에 대해서 설명해주세요.
ALD는 Atomic Layer Deposition으로 원자층 증착법입니다. 보통 많이 알려진 Chemical Vapor Deposition, CVD는 화학적 반응을 수반하여 막질을 형성하는데, ALD는 한층씩 원자수준의 1옹스트롱 내외로 박막을 증착합니다. CVD는 공정온도와 반응 gas의 부분합에 따라서 depo. rate을 조절할 수 있습니다. ALD 대비 100배 크게는 1,000배 빠르게 성장시킬 수 있어 Throughput이 높습니다. ALD는 CVD 대비 throughput은 낮지만 한 층씩 쌓기 때문에 우수한 step coverage와 막질의 다면적으로 균일하다는 장점이 있습니다.
[꼬리 1-1]. ALD도 CVD와 마찬가지로 Precursur와 반응 gas를 주입하는데, 왜 CVD와 차이가 나는지 설명해보세요.
ALD도 CVD와 마찬가지로 Precursor와 반응 gas를 주입하여 표면에서의 화학반응을 통해 막질을 형성하는 메커니즘을 갖습니다. CVD는 화학반응을 일어나기 전에 Precursor를 주입하고, 유기 또는 급속유기화합물 (MOCVD) 또는 화학반응을 필요로 하는 반응가스를 보통 2가지를 함께 주입하여, 공정온도, 압력, 혹은 플라즈마의 에너지를 이용하여 박막을 성장시킵니다. ALD 또한 precursor와 반응 gas의 화학반응으로 박막을 형성하지만 하나의 챔버 내에 동시에 두 가지 반응소스를 주입하는 것이 아닌 독립적으로 분리해서 precursor와 reactant를 시간적으로 (시분할 방식) term을 가지고 주입해줍니다.
[꼬리 1-2]. ALD의 단점과 개선사항에 대해서 설명해보세요.
기존 ALD의 방식은 Precursor와 reactant를 시간 term을 가지고 주입하는 시분할 방식으로 박막을 형성합니다. 하지만 이러한 ALD 방식은 우수한 박막 특성에도 불구하고 throughput이 낮다는 이슈를 안고 있습니다. 그래서 나온 방식이 '공간분할방식'입니다. 공간분할 방식은 분리된 공간이 있고, 웨이퍼가 그 공간으로 움직이고 그 다음에 반응가스인 precursor와 reactant가 계속해서 나오는 방식입니다. 즉, 시분할은 시간으로 분할돼서 한 공간에서 precursor와 reactant가 시간 term을 가지고 나왔지만 공간분할방식은 공간을 분할하여 간격을 떨어트려서 반응가스가 각각의 공간에서 주입되어 박막을 증착합니다. 최근에는 이 두 방식을 조합한 '시공간 분할 ALD' 장비가 개발된 것으로 알고 있습니다.
[꼬리 1-3]. '시공간 분할 ALD'에 대해서 설명해보세요.
ALD의 특징인 '100% 표면반응'과 '자기포화반응 or 자기제한적 흡착'을 달성하기 위해서는 precursor와 reactant를 주입했을 때, 이 둘의 반응소스가 표면 외에 공간에서 만나지 않게만 공정 제어를 해주면 됩니다. 그래서 시간적으로, 그리고 공간적으로 분할하여, precursor와 reactant가 주입되어 100% 표면반응을 유도함으로써 박막을 형성하는 방식으로 시공간 분할 ALD라고 합니다.
[꼬리 1-4]. 반도체 미세공정에서 ALD가 필요한 이유에 대해서 설명해보세요.
미세화 트랜드에 따라 우수한 막질의 얇은 박막과 정확한 박막 제어가 요구되기 때문입니다. 반도체 소자의 dimension이 작아지면서 박막 두께는 점점 얇아지고 있습니다. 최근 5nm, 3nm tech node가 발표되면서 초미세 선단 공정이 개발되고 있는데 작은 면적 내에서 복잡한 적층구조의 소자를 제작하기 위해서는 정확한 두께 제어가 요구됩니다. CVD의 경우, 박막을 두껍고 빠르게 증착할 수 있어 Throughput이 높은 장점이 있지만, 미세공정으로 갈수록 더 정밀한 증착 공정이 요구되기 때문에 원자층 단위로 증착 가능한 ALD가 각광받는 것입니다. 예를 들어, Gate-All-Around, GAA 공정과 같이 복잡한 구조를 구현하기 위해서는 다면적으로 균일한 박막 증착 스펙을 가진 ALD가 사용될 수밖에 없다고 생각합니다.
[꼬리 1-5]. ALD가 GAA 공정에서 중요한 이유에 대해서 설명하세요.
최근 IMB과 삼성전자가 nanosheet를 적층으로 쌓아 채널 면적을 향상시켜 전류 performance를 극대화시킨 소자입니다. Gate-All-Around FET, GAAFET 소자 구조를 보면 nanosheet의 multi-channel들을 gate가 전면으로 감싸고 있는 구조입니다. GAAFET은 Multi-channel을 적층구조로 쌓는 것 이외에도 gate, source, drain이 이 작은 영역에 모두 존재합니다. 그렇기 때문에 작은 구조 내에서 소자 기능을 구현하기 위해 원하는 spec의 얇은 두께의 박막을 균일하게 증착하는 정밀한 증착기술이 요구됩니다. CVD로는 분명히 한계가 있으며, 이러한 Critical한 영역에서 ALD가 중요한 역할을 한다고 생각합니다.
[꼬리 1-6]. ALD 공정은 주로 어떤 용도의 박막을 증착하는데 사용하는지 설명하세요.
ALD는 현재 양산에서 많이 사용되고 있습니다. 특히 ALD로 D램, 로직, 낸드, 반도체 쪽 여러 공정에서 많이 사용되고 있습니다. 대표적으로 우리가 알고 있는 배선 공정에도 사용되며, barrier metal, gate insulator, high-k 소재, capacitor의 절연체 등 굉장히 많이 적용되고 있습니다. 이 역시, ALD가 전면에 균일하고 얇은 박막을 증착할 수 있다는 이점 때문인 것 같습니다.
[꼬리 1-7]. Plasma ALD에 대해서 설명하세요.
저는 Thermal ALD 장비를 이용하여 박막레시피를 작성했던 경험이 있습니다. 기존의 Thermal ALD는 heating jacket을 이용하여 가열함으로써 열에너지를 통해 ALD의 반응 소스인 precursor를 활성화시킵니다. Plasma ALD는 반응소스의 활성화에너지를 열에너지가 아닌 Plasma를 통해 에너지를 전달하는 것입니다. Plasma 에너지를 사용할 경우, 고에너지의 plasma로 인해 반응소스의 다각화가 가능하며, 가장 큰 장점은 바로 '저온 공정'이 가능하다는 것입니다. 한 예로, FinFET 공정 시, Multi-patterning 공정에서 도포한 photoresist 위에 100℃ 이하의 저온에서 Plasma ALD를 통해 산화막을 형성해줍니다. 보통 유기물은 100℃ 이상에서 구조적 변화가 생기는 낮은 열적안정성을 가집니다. PEALD는 저온에서도 다양한 topology를 가지는 전면에 균일한 박막을 성장할 수 있다는 큰 장점을 가지고 있습니다.
반응형
그리드형(광고전용)
'반도체사관학교 훈련과정 > 반도체 전공정' 카테고리의 다른 글
[증착공정] 훈련 10 : "PVD 공정에 대해서 설명하세요" (5) | 2022.02.15 |
---|---|
[식각공정] 훈련 1 : "Etching 공정, 용어정리" (2) | 2022.02.15 |
[증착공정] 훈련 8 : "Atomic Layer Deposition, ALD에 대해서 설명하세요" (19) | 2022.02.14 |
[증착공정] 훈련 7 : "Chemical Vapor Deposition, CVD 불량 사례 분석" (0) | 2022.02.14 |
[증착공정] 훈련 6 : "MOCVD에 대해서 설명하세요." (4) | 2022.02.13 |
최근댓글