반응형
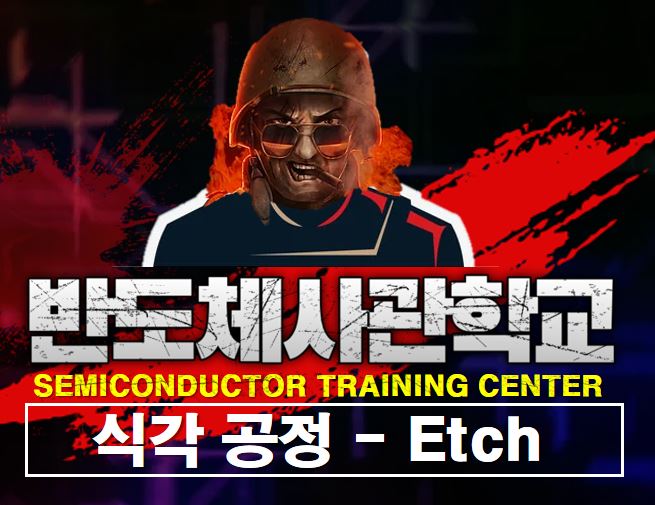
미세 공정이 기업 경쟁력이 되면서 Etch 공정의 기술력이 정말 중요해지고 있습니다. 그 이유는 박막을 Etching 하기 위해서는 메커니즘, 설비 이슈 뿐 아니라 Target 박막에 대한 적절한 Chemistry가 있어야 하기 때문이죠. 오늘은 이 부분에 대해서 다루어보도록 하겠습니다.
[질문 1]. Plasma Etch에 대해서 간략하게 설명해주세요 [복습]
Plasma Etch는 화학적으로 반응성이 높은 Gas에 의해 표면의 원자가 휘발성ㄹ 화합물을 형성하면서 식각이 되는 방식입니다. 높은 Selectivity 특성을 가지지만 Etchant Gas의 조성이 화학적 반응성이 높을수록 등방성 식각 특성이 나타나 Undercut이 발생할 수 있기 때문에 이를 제어하기 위한 첨가가스가 요구됩니다. 간단하게 메커니즘을 말씀드리면, Main Gas가 Chamber 내부로 주입되면 Plasma에 의해 활성화 에너지가 높아지며, Wafer 표면으로 확산되어 흡착됩니다. 흡착된 반응종은 표면에서 반응이 일어나고, 반응이 끝나면서 생성된 휘발성 화합물은 탈착되어 Gas Stream으로 확산되어 Chamber 외부로 나가게 됩니다.
[질문 2]. Conductor & Dielectric Etch에 대해서 설명하세요.
Conductor를 Etching 할 시에는 일반적으로 ICP Type의 Plasma Source를 사용합니다. Conductor Etching은 3D Profile 구현 시 윗면 뿐 아니라 Side에서도 Etching이 일어나야 하기 때문에 Plasma Density가 높은 ICP Type Plasma Source를 사용하는 것입니다. 대표적인 Dielectric 물질인 SiO2, Si3N4은 비교적 소재가 단단하기 때문에 높은 Energy의 Ion으로 Etching 해야 합니다. 그래서 ICP Type보다 에너지를 충분히 높힐 수 있는 CCP Type의 Plasma Source를 사용합니다.
① Conductor Etch, 예 : 텅스텐 W Etch 중요
Conductor를 Etching 할 때에는 주로 Etch 벽면에 Side Wall을 Control 하는 것이 매우 중요한 이슈입니다. Side Wall을 Etch Control 하기 위해서 주로 사용하는 방법론은 Gas 내에 Radical을 이용해서 Radical이 Etching 하고자 하는 Target 박막과의 화학적 반응이 아니라 Radical 반응 간에 화학적 반응으로 Polymerization을 유도해 Passivation Layer를 형성합니다. 그래서 Passivation Gas를 이용해서 Side Wall 방향으로 화학적 Etching이 되는 것을 억제함으로써 Vertical Profile을 구현할 수 있습니다.
어떤 Gas Chemistry를 사용할 것인지 선택 기준은 이전 장에서 설명드린 것처럼 '화학적 반응이 더 잘 일어나는 방향'으로 초점이 맞추어져 있습니다. 화학적 반응이 잘 일어나는 것의 판단 기준은 바로 'Boiling Point, BP'입니다. 흔히 사용하는 할로겐 가스 중에 텅스텐과 반응하여 형성되는 Byproduct 중에서 '어떤 Byproduct가 BP가 낮은지' 분석해보면 쉽게 알 수 있습니다.
WF6, WCl6, WOCl4 단순히 High Etch Rate을 목적으로 Etching 할 시에는 Cl보다는 원자량이 낮고 활성화 에너지가 높은 Fluorine, F가 유리합니다. F는 워낙 반응성이 높기 때문에 Etch Rate이 매우 높은 특성을 가집니다. 하지만 등방성 식각이 지배적이어서 Undercut의 이슈가 발생합니다. 따라서 이전 장에서 설명했듯이, Fluorine으로 Vertical Profile을 구현하기 위해서는 N2나, Cl2, H2 와 같은 추가 첨가 가스가 함께 주입되어야 합니다.
NF3/N2 + Cl2를 첨가할 경우, Chlorine에 의해 형성된 Byproduct가 Side Wall 쪽에 Passivation Layer를 형성하여 Fluorine의 Side Wall 방향의 Etch를 억제합니다. 따라서 Fluorine을 이용하여 Vertical Profile을 구현하기 위해서는 Fluorine과 Chlorine의 적절한 비율을 조합하여 사용합니다.
일반적으로 텅스텐을 Etching 할 때에는 상대적으로 Fluorine이 아닌 Chlorine을 사용합니다. 그 이유는 WF6보다 WCl6가 Boiling Point가 높아 Etch Rate잉 떨어질 수는 있지만, F에 비해 Vertical Profile을 구현하는데 훨씬 유리하기 때문입니다.
그리고 텅스텐을 Etching 하면서 추가적인 첨가가스들이 각각의 목적으로 첨가됩니다. 한 예로, 텅스텐을 에칭 시 Etching의 선택비를 높여주기 위해 Nitride 계열의 Blocking Mask가 존재하는데, 이 때 마스크가 함께 Etching 되면 원하는 Profile을 구현할 수 없기 때문에 Mask Loss를 줄이기 위해 O2 Gas를 함께 첨가해줍니다. Oxygen을 첨가하면 Mask가 Oxidation 되면서 텅스텐과 Mask의 Selectivity가 높아져 Mask Loss를 최대한 줄일 수 있습니다.
[질문 3]. 텅스텐 Etching 시 Fluorine과 Chlorine 계열 Gas를 사용할 때의 각각의 차이에 대해서 설명하세요.
Conductor를 Etching 할 때에는 Vertical Profile을 구현하기 위해서 Side Wall의 Etching을 Control 해야만 합니다. Etchant Gas의 Chemistry를 고려할 때에는 화학적 반응성을 고려하며 특히, Etching 시 형성되는 Byproduct의 Boiling Point, BP가 그 판단기준이 될 수 있습니다. Fluorine과 텅스텐이 반응하여 형성하는 WF6는 BP가 상대적으로 낮으며 이는 반응성이 높아 Etch Rate이 매우 크다는 것을 의미합니다. 하지만 Etch Rate이 높아지면서 등방성 식각이 이루어져 Undercut같은 이슈가 발생해 Vertical Profile 구현이 어렵습니다. 그래서 H2나 Chlorine과 같은 첨가 가스를 주입하여 Fluorine의 반응성을 낮추거나, Cl에 의해 형성된 Byproduct로 Sidewall의 Passivation Layer를 형성하여 Fluorine에 의해 Side Wall 방향으로 Etching 되는 것을 억제할 수 있습니다. Chlorine gas를 사용하면, 텅스텐과 반응하여 형성된 WCl6는 WF6보다 상대적으로 BP가 높고 이는 Fluorine보다 Etch Rate은 떨어지지만 그만큼 Vertical Profile을 구현하는데 유리하다고 할 수 있습니다.
[꼬리 3.1]. 텅스텐 Etching 시 Oxygen Gas의 역할에 대해서 명하세요.
Oxygen Gas는 Etchant Gas의 반응성을 높여 Etch Rate을 높이는 효과가 있습니다. (이전 교육 참고) 그 외에도 Oxygen Gas를 첨가하면 Selectivity를 높여 Blocking Mask의 Loss를 줄일 수 있습니다. 일반적으로 Etching 시 Photo 공정에서 형성한 PR 유기박막을 사용하지만 Narrow 하고 Vertical Profile을 구현하기 위해서 고에너지의 이온 충돌을 수반하기 때문에 Nitride 계열의 Hard Mask를 사용합니다. 이때, Mask가 함께 Etching이 되는 경우 의도치 않은 Profile이 구현되면서 Target 조건에 벗어나 수율 저하의 요인이 됩니다. 그래서 Oxygen Gas를 첨가하면 Mask Layer의 Oxidation을 통해 텅스텐과 Mask의 Selectivity를 높여 Mask Loss를 최소화 할 수 있습니다.
[꼬리 3.2]. Etch 공정에서 Gas Chemistry 외에 중요한 공정 변수에 대해서 명하세요.
Etch 공정에서 Gas Chemistry 뿐 아니라 공정 온도 또한 중요한 인자입니다. 온도를 높일 경우 Chlorine 계열 Gas로 Etching 시 Byproduct가 Fluorine에 비해 비휘발성 특성이 있어 Passivation Layer가 형성돼 Etch Rate을 저하시킵니다. 이때 공정 온도를 높이면, Passivation Layer가 쌓이더라도 쉽게 제거가 되는 효과가 있으며, 낮은 공정온도 대비 Vertical Profile 구현이 용이합니다. 그래서 Etch 공정 시 Gas Chemistry 뿐 아니라 공정 온도, 압력, 바이어스 파워, Plasma Source Type 등 다양한 공정변수를 통해 Etching 공정을 최적화시킵니다.
[Etch 공정 시 주요 변수]
① Gas Chemistry : F, Cl, Br이 Target과 반응하여 형성된 Byproduct의 Boiling Point 고려. [BP (↓) → Etch Rate (↑) → 심하면 등방성 식각에 의한 Undercut 이슈 / BP (↑) → Passivation (↑) → Etch Rate (↓)]
② Process Temperature : Side Wall 방향 비휘발성 Passivation Layer 형성 촉진 or 휘발성 Byproduct 제거
③ Pressure : 압력이 낮을수록 Mean Free Path (↑) → 깊은 곳까지 Ion과 Radical이 들어가면서 비등방성 식각. 압력이 높으면 Mean Free Path (↓) → Ion과 Radical이 방향성을 잃게 되면서 Vertical Profile 구현이 어려움.
④ Bias Power : Bias Power를 높임으로써, Ion의 Energy를 높임. 너무 강한 Bias Power는 Plasma Damage를 초래할 수 있으며, Ion 충돌에 의한 Etching 자체가 Selectivity가 낮기 때문에 Overcut이 발생할 수 있음.
⑤ Plasma Source Power : Plasma Source Power를 높일수록 Plasma Density가 높아지고, 이때 Etchant Gas에서 활성화된 Radical에 의해 Etch Rate이 높아지나, 심하면 등방성 식각이 일어날 수 있음.
[질문 4]. ICP Type과 CCP Type Plasma Source에 대해서 설명하세요.
Etching 공정에서 ICP Type은 주로 Conductor 박막을 CCP는 비교적 단단한 Dielectric 박막을 Etching 할 때 사용합니다. Plasma Etch 공정 설비 초기에는 CCP Type의 Plasma Source가 많이 사용됐습니다. 기본적으로 양쪽 전극 사이에서 발생하는 Plasma를 이용하는 CCP Type은 Plasma가 Density와 DC Voltage로 정의됩니다. 그렇기 때문에 Plasma Density와 Voltage를 따로 Control 할 수 없다는 단점이 있습니다. 그래서 현재의 미세 트랜드에 따라 점점 더 높은 Aspect Ratio의 구조를 요구하는 반도체 산업에서 CCP Type은 한계에 봉착하게 됩니다. 그래서 최근에는 Plasma Density와 Voltage를 따로 Control 할 수 있는 ICP Type Plasma Source가 사용되고 있습니다.
(이전에는 1-Step Etch시 High Aspect Ratio Etch Profile 구현 시, CCP 사용할 경우 Loading Effect의 이슈를 개선할 수 있었습니다. 그 이유는 CCP type Plasma Source의 경우, 낮은 Frequency에서도 Plasma를 발생시킬 수 있기 때문에, Etching시 반응에 의해서 생성된 Byproduct가 충분히 빠져나갈 수 있는 시간이 있습니다. 반면에 ICP Type은 Plasma Uniformity 문제와 High Freq. 를 사용하다 보니, Loading Effect에 자유롭지 않게 되었죠. 그러다 더욱 반도체가 미세해지면서, 반응에 의한 Byproduct가 빠져나갈 시간을 벌어주기 위해 기존 Continuous Wave에서 Pulsed 형태의 Plasma를 인가함으로써 Micro Loading Effect를 개선하는 기술이 개발되었죠)
[ICP Type vs. CCP Type]
ICP Type과 CCP Type은 이전 PVD 플라즈마 교육에서 심도있게 다루었던 것 같습니다.
ICP Type Plasma Source에 대해서 말씀드리자면, Maxwell 법칙에 의하면 도선에 전류가 흐르면서 그 주위로 도선에 수직한 방향으로 자기장이 형성됩니다. RF 전류는 교류이므로 유도딘 자기장 역시 시간에 따라 크기가 변하게 되고 그에 수직한 방향의 Electric Field가 유도됩니다. 그래서 자기장은 Coil이 감긴 방향과 같은 방향으로 형성이 됩니다.
(일반적인 전자기학 내용...ㅠ 가볍게 듣고 넘어가셔도 돼요~ㅎㅎ)
전자는 전기장 방향으로 회전운동을 하게 되고 전자의 운동 Path가 전극 내부에서 잘 격리되면서 전자의 Loss가 급감하게 됩니다. (CCP Type은 전극에서 전극으로 전자가 이동하기 때문에 ICP Type에 비해 전자 Loss가 상당히 큼.) 그렇기 때문에 전자가 회전 운동을 하면서 챔버 내부의 기체원자와 충돌할 확률이 커지게 되어 Plasma의 Density를 높힐 수 있는 것입니다. (이러한 이유로 CVD에서도 High Density Plasma CVD, HDPCVD에서도 ICP Type의 Plasma Source를 사용합니다!) ICP Type의 장점은 이러한 전자의 회전운동으로 전자 Loss를 감소시켜 Plasma Density를 높일 수 있으며, 한 가지 더 큰 장점은 바로 Low Pressure에서도 Plasma Density를 유지할 수 있다는 것입니다. 또한 Substrate 하단에 Back Bias를 인가할 수 있어 ICP Type은 Plasma Density와 DC Voltage를 따로 제어할 수 있습니다. (HDPCVD에서도 동일하게 적용되어 Depo-Etch-Depo를 반복하여 우수한 Step Coverage를 구현할 수 있었음. 정말 잘 따라와주셔서 감사합니다. 교육생 여러분..)
위에서 설명드린 공정변수 중에 저압에서 Etching을 진행하면 Mean Free Path가 길어지면서 더 깊숙히 Ion과 Radical이 들어가 Narrow Vertical Profile을 구현할 수 있다고 했습니다. 하지만 이전 PVD Plasma 강의에서 말씀드렸듯이 파센법칙을 살펴보면 챔버 내부의 압력이 낮을수록 기체원자의 수가 적어지면서 Glow Discharge를 일으킬 수 없어 Plasma를 유지할 수 없는 상황에 이르게 됩니다ㅎ. (우리 딴딴 취준 여러분들 여기까지 잊지 않고 따라오셨다면 정말 대단! 대단!)
이러한 이유로 ICP Type의 Plasma Source가 최근 High-Tech에서는 더 많이 사용되고 있습니다. 하지만 이러한 ICP Type의 Plasma Source 또한 이슈가 존재합니다. 그것은 전자의 회전운동으로 전극 사이에 Loss를 줄여 Plasma Density를 높일 수는 있지만, 회전운동을 하다보니 Plasma가 전자의 Path에 따라 형성이 되고, 도넛츠 모양으로 Plasma가 형성되어 Plasma의 Uniformity가 저하됩니다. 이는 분명히 Etching과 Deposition에서 악영향을 미치며, 이를 개선시키기 위해서 Plasma 기술 개발이 더욱 중요해지고 있습니다.
CCP Type Plasma Source는 두 전극에 Bias를 인가하기 때문에 Electron의 방향이 전극방향이고 전극으로 들어가는 전자에 의해 Electron Loss가 큽니다. 평평한 전극이 평행한 구조로 전극 위에 Wafer가 위치하고, 두 전극 간에 인가된 Bias에 의해 Electric Field가 형성되고 Glow Discharge를 일으킵니다. CCP Type의 이점은 이온에너지를 충분히 높일 수 있고, 동작이 간단하며, 대면적으로 공정이 가능합니다. 하지만 Plasma Density와 Sheath 전압을 따로 Control 할 수 없어 복잡한 구조의 Etching 공정에서는 불리하다는 단점이 있습니다. 하지만 CCP Type의 이온에너지를 충분히 높일 수 있다는 장점은 단단한 박막인 Dielectric Etching 시 유리합니다.
정리하자면 ICP Type은 높은 Plasma Density를 저압에서도 형성 가능하고, Back Bias를 인가하여 Sheath Voltage를 따로 제어할 수 있어 3D 구조의 복잡한 Profile Etching 시 사용되며, CCP Type은 Ion Energy를 높일 수 있어 Dielectric Etching 시 주로 사용됩니다.
하.. 여러분들 Etching 공정 불태웠습니다. 오늘은 Conductor 와 Dielectric Etching에 대해서 다루어보았습니다. 다음 시간에는 Dielectric Etching에 대해서 좀 더 자세히 다루고, Etching시 발생하는 이슈와, 차세대 Etching 기술에 대해서 다루어보도록 하겠습니다.
오늘 하루도 고생 많으셨습니다. 모두 코로나 조심하시고.
꼭 취업이 아니더라도 성장한다는 생각으로 교육에 임하셨으면 좋겠습니다.
충성! From. 교관 홍딴딴
반응형
'반도체사관학교 훈련과정 > 반도체 전공정' 카테고리의 다른 글
[식각공정] 훈련 7 : SiO2, Si3N4 Etch Rate & 결정면에 따른 Etch Rate (16) | 2022.04.13 |
---|---|
[식각공정] 훈련 6 : Depth Loading Effect / Blocking Mask 이슈 (32) | 2022.04.12 |
[식각공정] 훈련 4 : "Reactive Ion Etching, RIE 공정에 대해서 설명하세요" (16) | 2022.04.11 |
[식각공정] 훈련 3 : "Dry Etching, 건식 식각 공정에 대해서 설명하세요" (19) | 2022.04.11 |
[Yield] : PCM, SPICE Modeling, Corner Margin 평가 (0) | 2022.04.01 |
최근댓글